Slavik Marinovski, Machinix technical solution engineer, talks with Roger Senden from RSP Technology about the aluminum super-alloys they produce and its uses in precision equipment manufacturing, including:
- How it’s made
- Their usage in the semiconductor and other precision equipment industries
- Slavik’s experience machining it
- Tool wear and cost effects
Q&A
When does low thermal expansion material needed?
Thermal expansion is the tendency of matter to increase in length, or volume, changing its size and density in response to an increase or decrease in temperature.
Low thermal expansion alloys are essential in applications requiring high dimensional stability across temperature changes, in order to achieve a part or a system’s stability, reduce potential stress or damage, so that temperature fluctuations are of little concern to consistent performance.
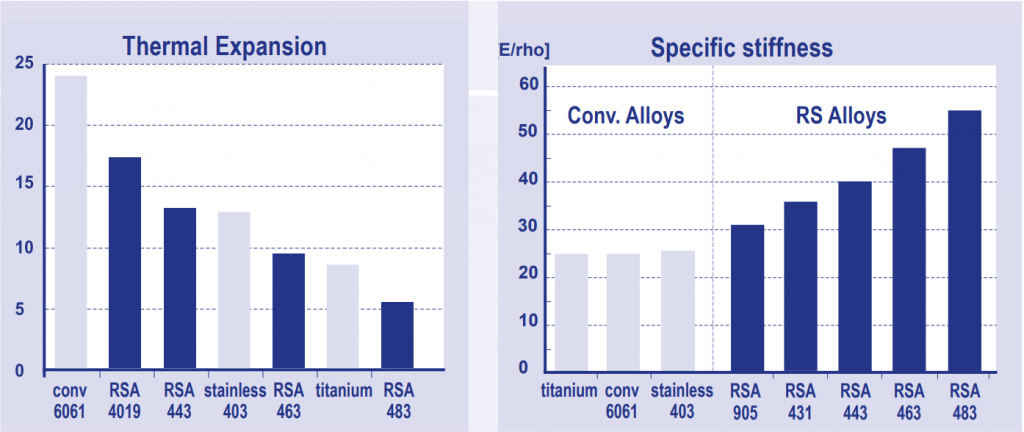
What is RSP technology?
RSP Technology produces and develops aluminum superalloys.
The company specializes in producing and developing aluminum superalloys using an ultra-rapid cooling technology that solidifies liquid metal at over 1,000,000ºC per second. This process creates super-strong alloys with a fine, homogeneous microstructure. Their melt-spinning method results in unique materials ideal for high-end applications in aerospace, optics, precision equipment, racing, electronics, medical, and automotive industries. The Rapid Solidification Process (RSP) allows for extensive alloying possibilities and efficient production cycles.
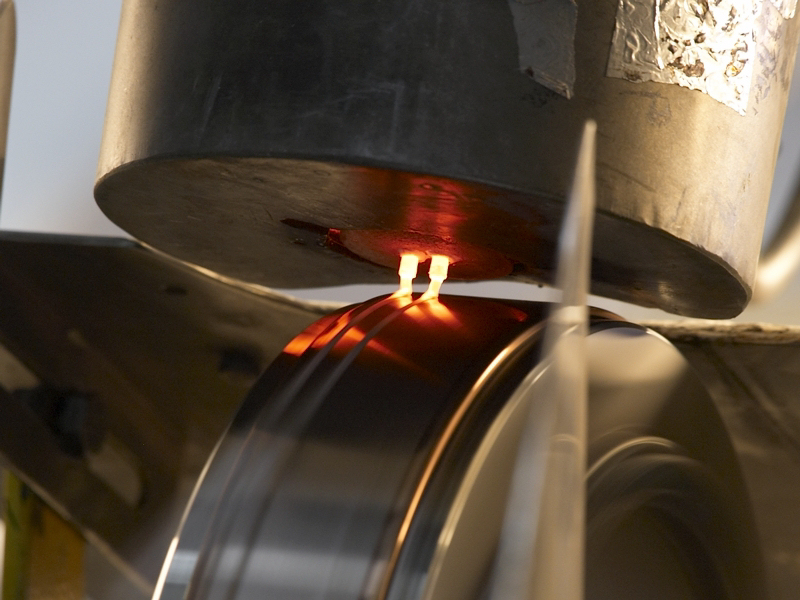
RSA443 Vs. AL 6061 Vs SS 304
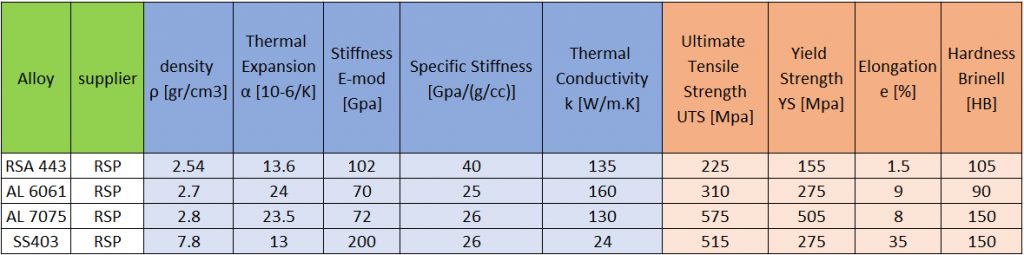
Which industries can benefit from using RSP Alloys?
In the below specified industries, several systems require low thermal expansion alloys to maintain high performance and reliability:
- Semiconductor industry: In semiconductor metrology, components like baseplates, frames, stages, optical mounts, and probe arms benefit from low CTE, high stiffness, and low weight materials, which ensure stability, precision, and minimal thermal drift. they can benefit from reduced vibrations and support fast, precise positioning in critical measurement tools. These properties are essential for minimizing errors caused by thermal expansion, and ensuring consistent performance across varying conditions.
- Medical Devices: MRI machines, CT scanners, and high-precision surgical tools. These systems depend on low thermal expansion materials to prevent deformation and maintain accuracy across temperature variations.
- Aerospace: Satellite components, mirrors, and support structures for telescopes.
- Precision Instruments: Telescope mounts, precision measurement equipment, and high-accuracy scales.
- Fine Motion Systems: These systems, such as those used in robotics and automated manufacturing, require materials that maintain their dimensions under varying temperatures to ensure accurate movement and positioning.
- Lasers: Optical components in laser systems, like mirrors and lenses, need to retain their precise shapes to maintain beam quality and focus. Any thermal expansion could lead to misalignment and degraded performance, affecting tasks like cutting, engraving, or communication.
What are the Is there any limitation on material shape availability?
- RSP alloys can be produced in the following standard dimensions:
- Bars: diameters 18, 22, 26, 35, 45, 60, 65, 85, 105 mm
- Billets: diameters 165, 200, 290, 360, 420, 500, 600, 800, 1.000 mm
- Custom made (near net) forgings and rectangular blocks
- Any other size can be custom made in round, rectangular or any other shape up to approximately 1000mm (39.37”)
What are the different alloys produced by RSP?
These are some of the alloys produced by RSP, their characteristics and use cases:
- RSA-443 (Al Si40): This alloy offers high dynamic and thermal stability (high conductivity, low expansion), and high damping. Its fine microstructure makes it ideal for precision equipment and diamond-machined/polished mirrors.
- RSA-461 and RSA-611: These alloys possess high-temperature strength, making them suitable for piston applications. Their low thermal expansion allows for tighter piston-cylinder fits, resulting in a CO2 emission reduction of at least 20%. Additionally, the increased combustion temperature possible in high-performance diesel engines further saves energy and reduces CO2 emissions.
- RSA-905: This alloy boasts particularly high strength and stiffness (about twice that of aluminum alloy 6061). It’s useful for structural components in machine building, medical equipment (as a titanium replacement), measuring equipment, hydraulic systems, and more.
When is stress release recommended?
It is recommended to apply stress release after rough machining, when the machined part requires tight tolerances in the range of 0.01-0.03mm, and when there is substantial material removal from the raw material.
for example RSA-443 alloy can be artificially aged using the following process:
- Rough machine to within 0.2-0.5mm of final dimensions.
- Put the part in a cooled furnace, at room temperature (20 – 25 ºC).
- Heat the part gradually to 380±5 ºC, at a rate of 100ºC per hour.
- Keep the part at a stabilized temperature of 380±5 ºC, for 2 hours.
- Cool the part to room temperature (20 – 25 ºC) slowly, in a closed furnace.
Following this process, a final finish machining can be performed.
Recent Comments